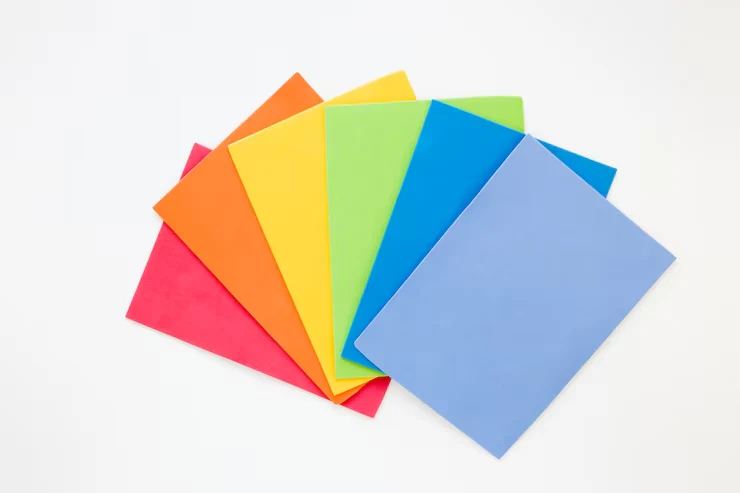
How to Select the Right Gasket Material for High-Pressure Applications
In high-pressure systems, even a minor leak can lead to significant operational risks, safety hazards, and financial losses. That’s why selecting the right gasket material for high-pressure applications is critical for maintaining safe and efficient performance in pipelines, valves, and flanges. Whether you're working in oil & gas, petrochemicals, or power plants, choosing a gasket that withstands pressure, temperature, and chemical exposure is non-negotiable.
In this guide, we’ll explore how to choose the right gasket material based on operating conditions, material properties, and application-specific demands.
Why Gasket Selection Matters in High-Pressure Systems
Gaskets serve as the critical sealing element between two mating surfaces, preventing leakage of gases or fluids under high pressure. In demanding environments, the wrong gasket material can lead to:
- Premature seal failure
- Flange distortion
- Safety incidents due to leaks
- Increased maintenance costs
That’s why high-pressure applications need specialized gasket materials engineered to resist compression, pressure cycling, and thermal stress.
Key Factors to Consider When Choosing Gasket Material
1. Operating Pressure and Temperature
High-pressure environments (above 600 PSI) often coincide with high temperatures. Gasket materials must maintain sealing integrity without creeping or deforming.
- Recommended materials: Spiral wound gaskets, RTJ (Ring Type Joint) gaskets, and compressed non-asbestos fiber (CNAF).
2. Chemical Compatibility
The gasket material must be chemically compatible with the process fluids or gases. A mismatch can lead to degradation and leakage.
- For acids and corrosive chemicals: PTFE-based or graphite gaskets are ideal.
- For hydrocarbons: Non-asbestos or metal-reinforced gaskets work well.
3. Flange Surface and Load
Not all flanges have the same surface finish or bolting force. Softer materials like rubber may work on low-load systems, while high-pressure flanges require stronger gaskets.
- Metal gaskets (like RTJ) require high flange pressure to seat properly.
- Soft gaskets can be compressed with lower torque but are unsuitable for extreme pressure.
4. Application Type
Each industry has different requirements. For instance:
- Steam systems need gaskets that can handle temperature and water pressure—like graphite.
- Gas pipelines require blowout-resistant gaskets—like spiral wound or metal-jacketed ones.
Common Gasket Materials for High-Pressure Applications
Material | Ideal Use Case | Pressure Range |
Spiral Wound | Oil & gas, petrochemicals, refineries | Up to 10,000 PSI |
Graphite | High temperature, steam, acidic environments | Up to 5,000 PSI |
PTFE (Teflon) | Corrosive chemicals, low-friction sealing | Up to 3,000 PSI |
Metal Jacketed | Heat exchangers, boilers, reactors | Up to 6,000 PSI |
RTJ (Ring Type) | Critical sealing in flanged connections (offshore, pipelines) | 5,000–20,000 PSI |
Signs of Gasket Failure in High-Pressure Applications
Monitoring gasket performance is key. Look out for:
- Loss of torque or tension
- Visible leaks at the joint
- Discoloration or burning around the seal
- Frequent need for re-tightening
These are signs that you may need a stronger material or re-evaluation of your torque/load application.
Best Practices for Gasket Installation in High-Pressure Systems
- Ensure proper surface finish – A smooth flange face ensures better sealing.
- Use calibrated torque wrenches – Prevents over-tightening or uneven compression.
- Follow the star bolt tightening sequence – This distributes load evenly across the gasket.
- Avoid reusing gaskets – Always install new gaskets to prevent material fatigue.
- Store gaskets properly – Away from sunlight, chemicals, or moisture.
Conclusion
Selecting the right gasket material for high-pressure applications is not just about sealing—it's about performance, safety, and long-term reliability. Understanding your system’s pressure, temperature, and fluid characteristics will help you choose between spiral wound, graphite, PTFE, or metal-jacketed gaskets. For critical environments, consult with experts to ensure your sealing solution is engineered for success.
At
Al Kun Steel
, we supply a wide range of high-performance gaskets suitable for every industrial requirement—from offshore pipelines to chemical processing units. Explore our gasket solutions to find the right fit for your next project.